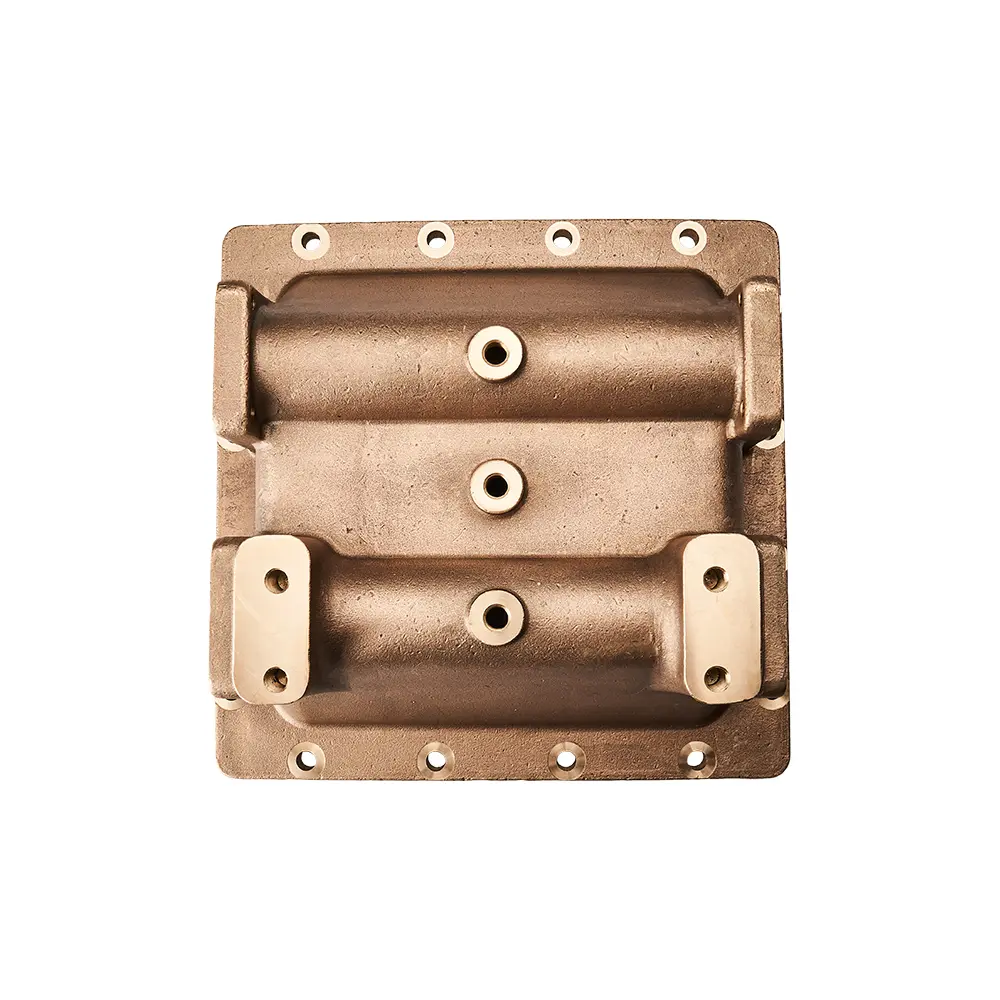
Top 5 Copper Alloy Precision Casting Suppliers in Asia
Copper alloy Precision Casting plays a vital role in industries that demand durable and accurate components. You rely on this process to create parts with exceptional strength and intricate designs. Manufacturers in Asia have mastered this craft, combining advanced technology with years of expertise. Their commitment to precision ensures that you receive high-quality products tailored to your needs. Whether for automotive, aerospace, or industrial applications, copper alloy precision casting delivers unmatched reliability and performance.
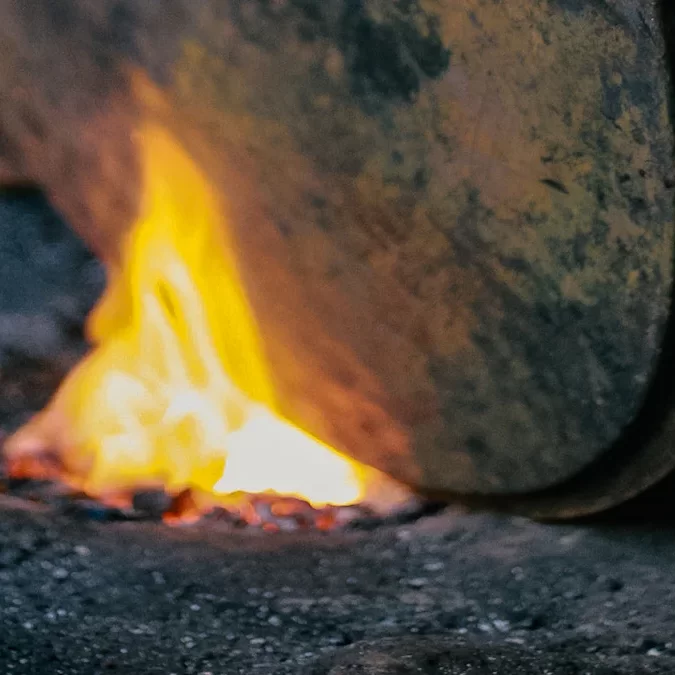
How Roasting Shapes Investment Casting Success
The roasting process plays a pivotal role in Investment Casting. It strengthens the ceramic shell, enabling it to endure extreme temperatures during metal pouring. This step ensures the mold achieves optimal porosity and thermal stability, which are essential for producing flawless castings. Manufacturers rely on precise roasting techniques to eliminate residual wax and moisture, preventing defects in the final product. By mastering this process, they enhance the durability and reliability of molds, setting the foundation for high-quality results.
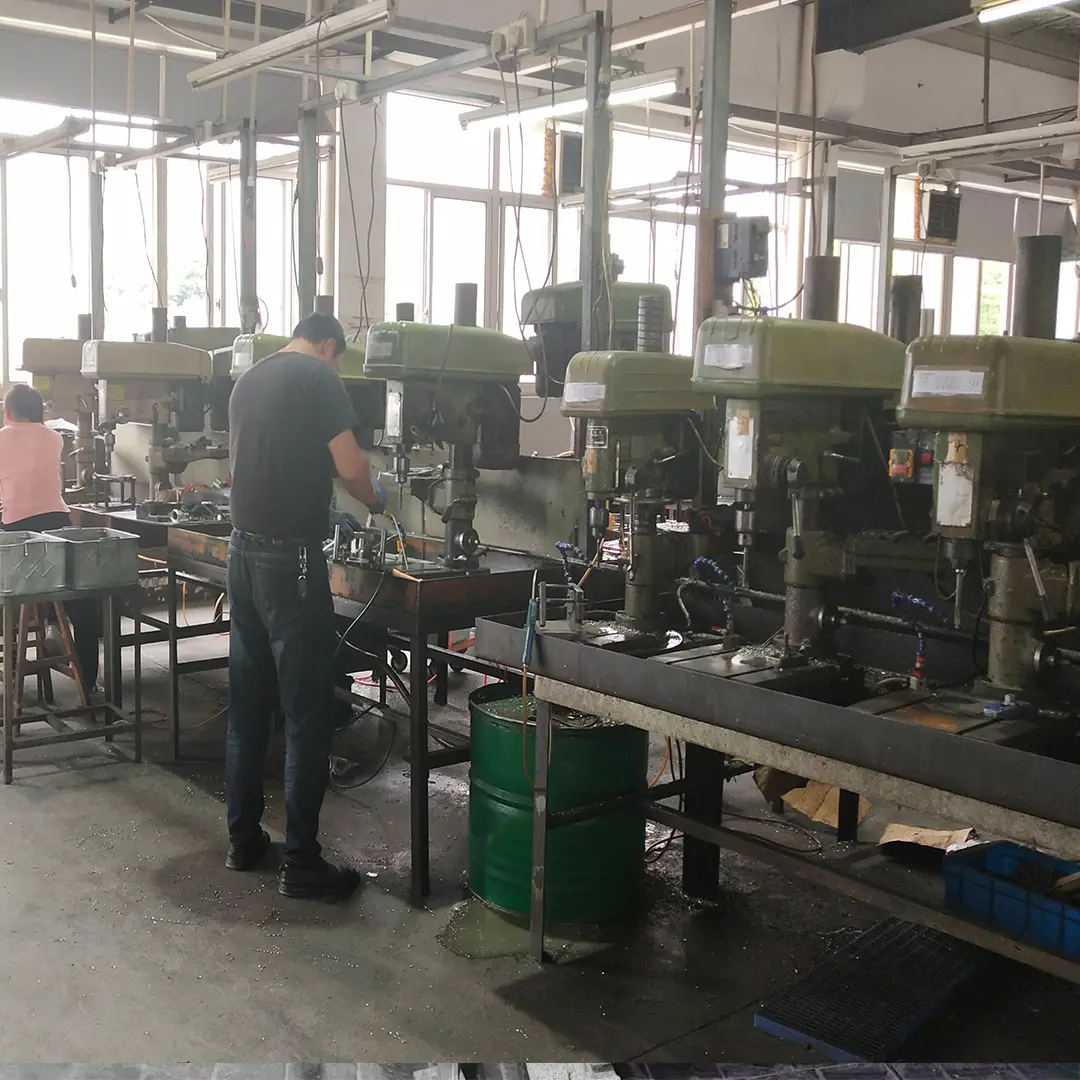
Understanding Silica Sol Precision Casting for Copper Alloys
Silica sol precision casting offers a cutting-edge solution for creating intricate components. This method uses silica sol as a binder, ensuring high precision and exceptional quality. You can rely on this process to produce detailed copper alloy parts with remarkable accuracy. Its ability to deliver superior results makes it ideal for industries that demand precision and efficiency. For example, flange bearing housing-silica sol precision cast copper Alloy Casting demonstrates how this technique excels in manufacturing complex and durable components. As industries evolve, this casting method continues to gain importance for its reliability and cost-effectiveness.
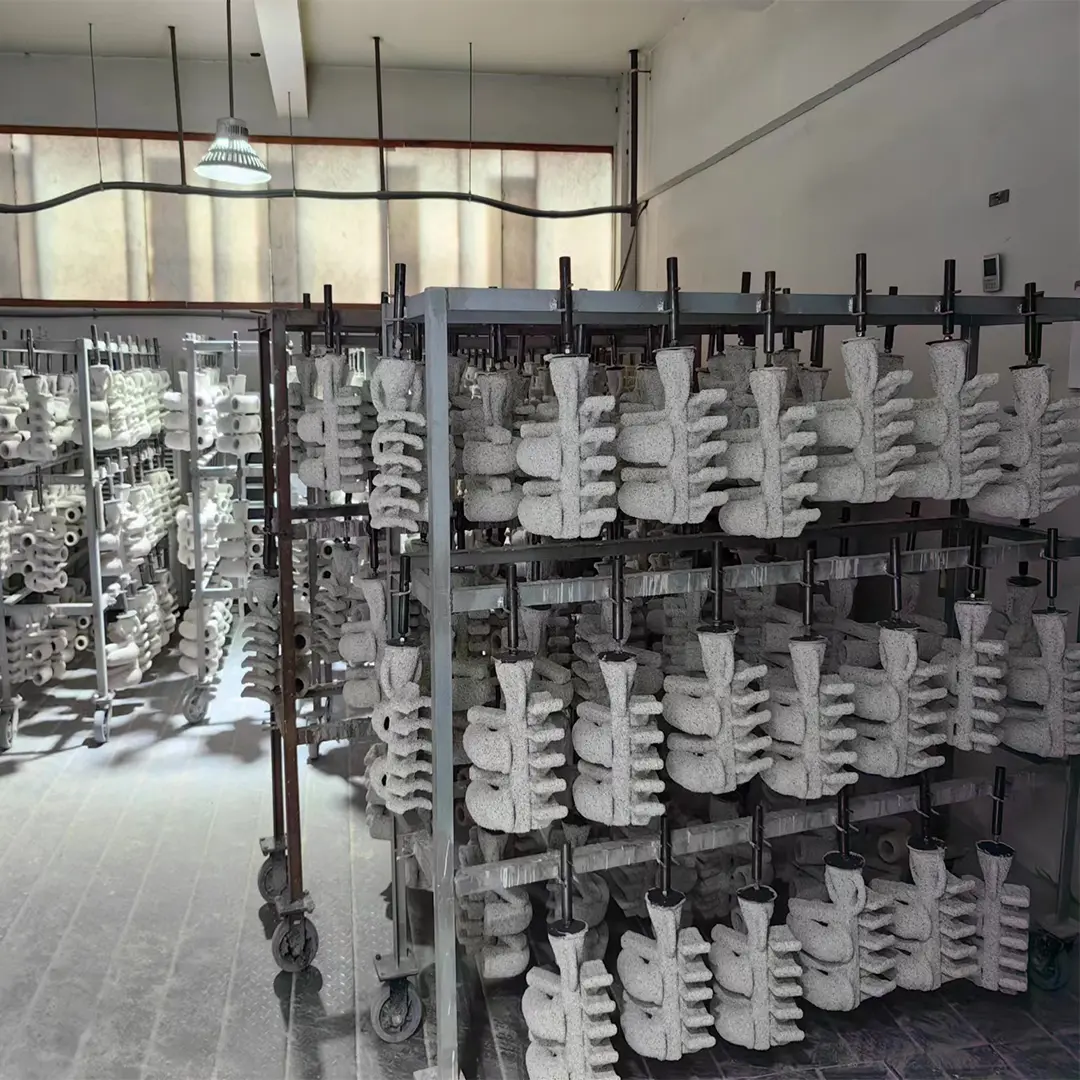
Stainless Steel Precision Castings: Which Method Wins
Stainless steel precision castings play a crucial role in modern manufacturing. The choice of casting method depends on factors like design complexity, production volume, and cost. Each method offers unique advantages tailored to specific needs. For instance, some methods excel in creating intricate designs, while others prioritize efficiency for large-scale production. Understanding these differences helps manufacturers achieve optimal results. Selecting the right method ensures better performance, durability, and cost-effectiveness in the final product.
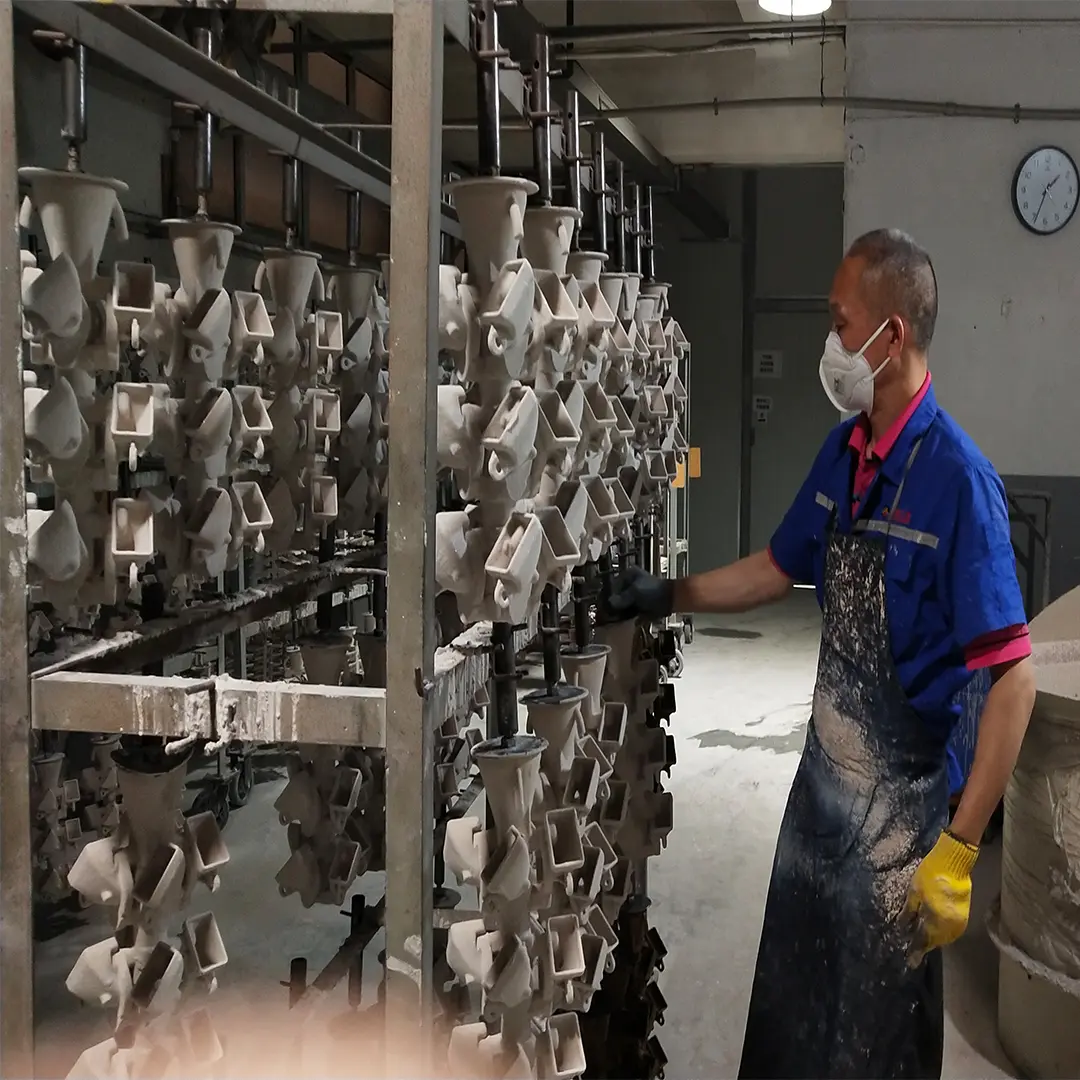
Discover Why Brass Precision Castings Dominate Today
Brass precision castings stand out as a remarkable solution for precision casting due to their unique properties. The malleability of brass allows you to create intricate designs with ease, while its natural corrosion resistance ensures durability in challenging environments. The dimensional stability of brass guarantees precise and reliable components for various applications. Additionally, brass precision castings offer exceptional versatility, making them suitable for industries ranging from automotive to decorative arts. Their cost-effectiveness and aesthetic appeal further enhance their value, providing you with a material that combines functionality and beauty seamlessly.
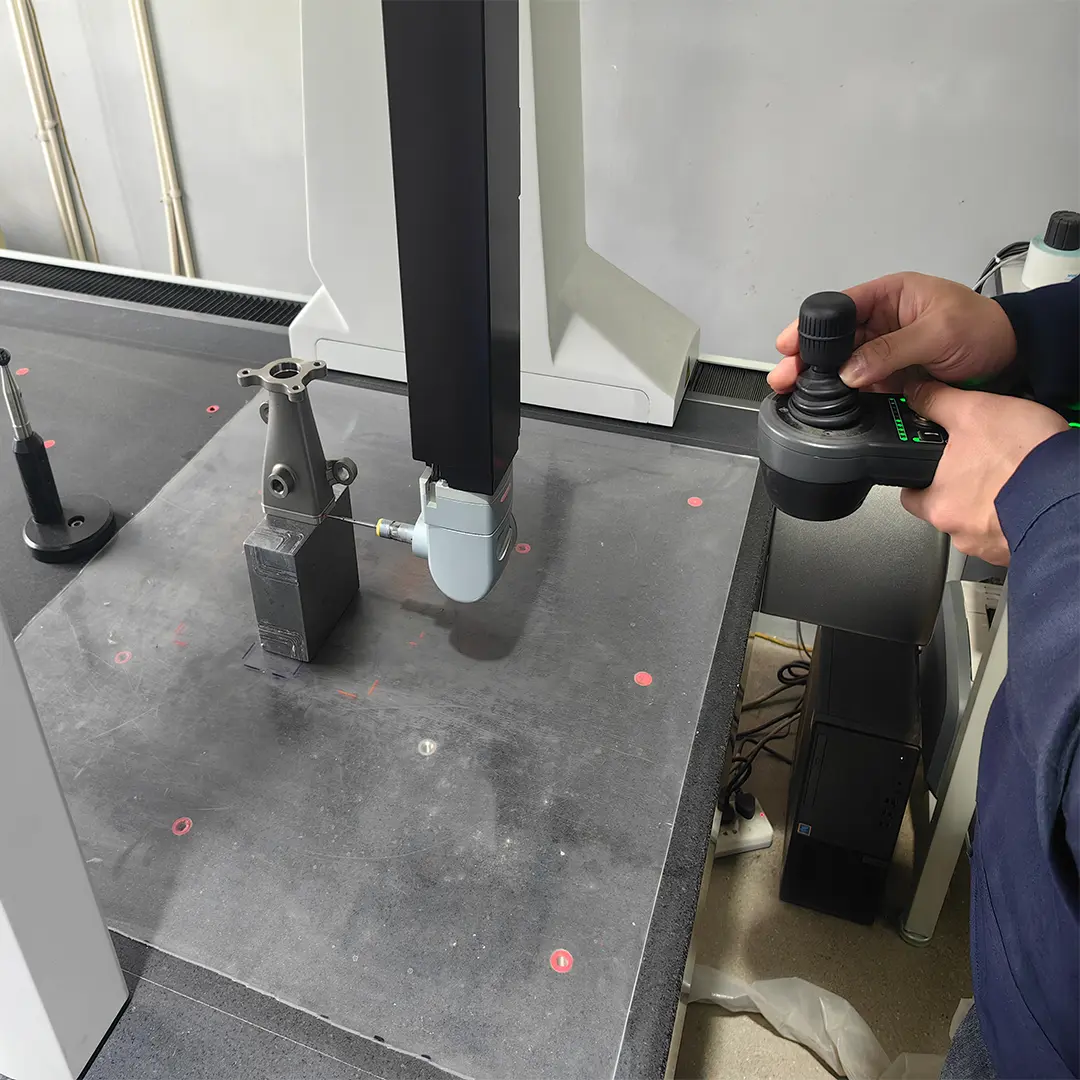
Die Casting vs Investment Casting for Copper Components
Die casting and investment casting serve as two essential methods for producing copper precision components. Each method offers unique benefits and challenges, making the selection process critical for manufacturers. Die casting supports high-volume production with consistent quality, while investment casting enables intricate designs with superior precision. For applications like inlet and outlet chambers-copper precision castings, understanding these methods ensures optimal performance and cost-efficiency. The choice directly influences the final product's quality, durability, and suitability for industrial use.
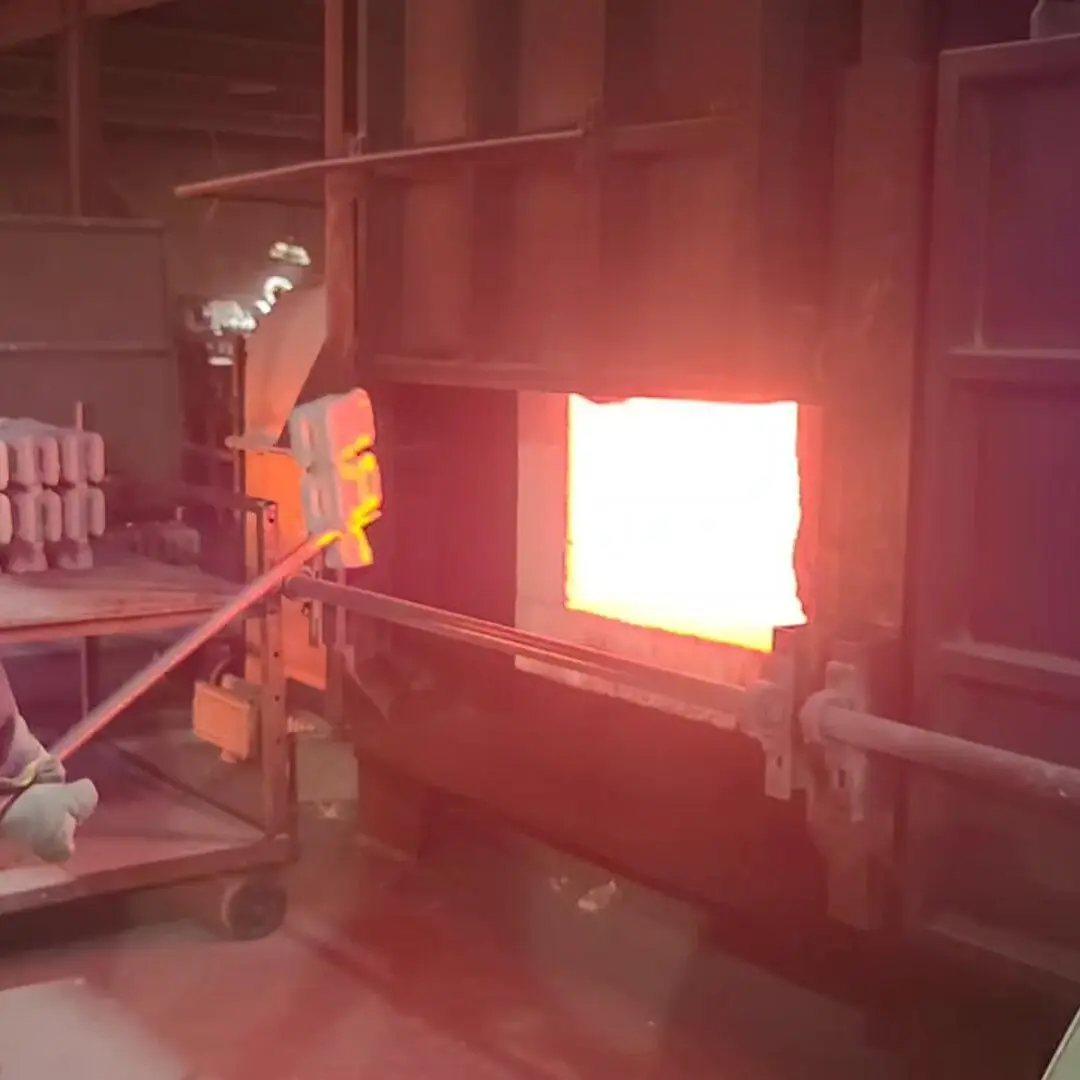
Investment Casting Made Simple: Roasting Process Highlights
The roasting process plays a critical role in investment casting. It prepares the mold by eliminating residual wax and moisture, ensuring it can withstand the demands of metal casting. This process strengthens the mold, making it capable of handling high temperatures and maintaining its shape during casting. By properly roasting the mold, you ensure the production of precise and durable metal components. Skipping or mishandling this step can compromise the quality of your final product, leading to defects or inefficiencies.
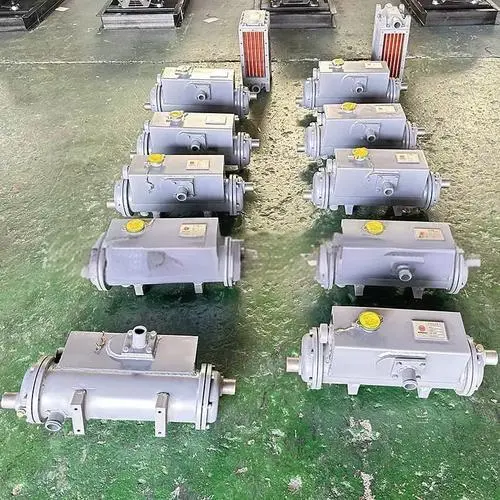
How Tin-bronze Precision Castings Improve Heat Exchangers
Tin-bronze precision castings revolutionize the performance of heat exchangers by delivering unmatched material benefits. Their exceptional corrosion resistance ensures durability in both seawater and freshwater environments, where other materials often fail. High thermal conductivity enhances heat transfer efficiency, a critical factor in industrial applications. Additionally, their mechanical strength supports long-term reliability under demanding conditions. Precision casting techniques further refine these components, enabling intricate designs and superior accuracy. These qualities make tin-bronze precision castings indispensable for industries requiring robust and efficient heat exchanger solutions.
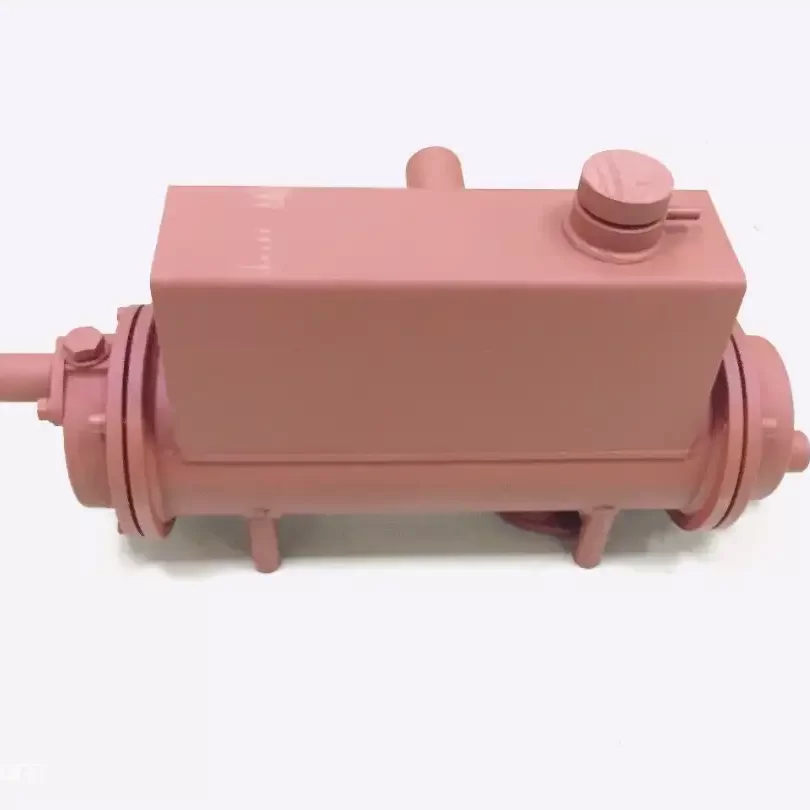
How Tin-bronze Precision Castings Boost Heat Exchanger Durability
Heat exchangers in marine and freshwater systems face constant exposure to corrosive environments. Tin-bronze precision castings offer a reliable solution by enhancing their durability and performance. This alloy resists corrosion effectively, even in harsh seawater conditions. Its mechanical strength ensures the components withstand high pressures and demanding operations. Additionally, its excellent thermal conductivity optimizes heat transfer efficiency. These properties make tin-bronze precision castings an indispensable choice for industries seeking long-lasting and efficient heat exchanger solutions.
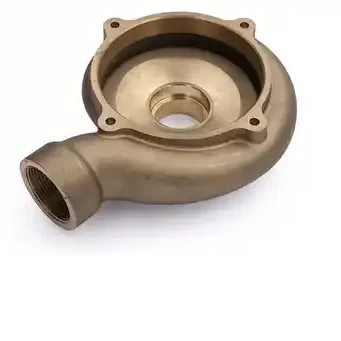
Top 5 Bronze Precision Casting Suppliers in China
Finding the right supplier for bronze precision casting is crucial for ensuring high-quality results and efficient production. China stands out as a hub for top-tier suppliers in this industry. Among the best are CFS Foundry, Ningbo Pingheng Machinery Co., Ltd., Dongying Changrui Investment Casting Co., Ltd., Taiyuan Simis Investment Casting Co., Ltd., and a reputable supplier from Alibaba. These companies deliver exceptional craftsmanship and reliable services. Choosing a trusted partner not only guarantees superior products but also enhances your business operations by meeting your specific needs with precision.